Découvrez le Toyota Production System (TPS), système socio-technique développé par Toyota pour organiser la fabrication et la logistique.
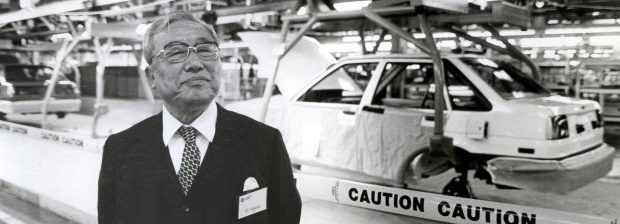
Le Toyota Production System (TPS) efficacement organise la fabrication et la logistique, minimisant les coûts et les déchets tout en favorisant une interaction fluide avec les fournisseurs et les clients.
La philosophie du système de production Toyota consiste à « tirer » un produit fini d’un bout à l’autre de la chaîne de production. Les pièces détachées sont approvisionnées au bon endroit, au bon moment, et en quantités suffisantes, sans gaspillage.
À lire aussi sur dondon.media : 🏯 Les entreprises les plus anciennes du monde sont au Japon et l’explication va vous étonner
Ce dernier permet d’augmenter le flux de trésorerie et de réduire les besoins en espace physique, et facilite la livraison des résultats requis en douceur par le biais de processus internes, une pièce à la fois (single piece flow) jusqu’au client final.
Le TPS a joué un rôle déterminant dans le succès de Toyota en tant que leader mondial de la fabrication automobile, révolutionnant l’industrie avec son système intégré de contrôle qualité.
Initialement développé entre 1948 et 1975 en réponse à la crise de l’après-guerre, le TPS a été influencé par des figures clés telles que Sakichi Toyoda, Kiichiro Toyoda et l’ingénieur Taiichi Ohno :
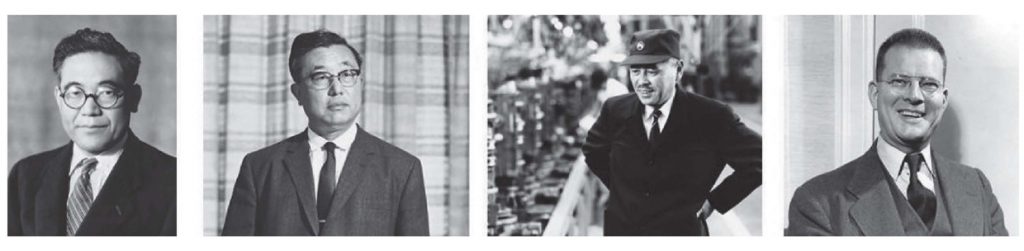
Dans les années 1950, l’entreprise a frôlé la faillite, mais après une transformation majeure, elle a connu une croissance constante des ventes et des parts de marché, sans année non rentable. La visite d’Eiji Toyoda (ingénieur et membre de la famille fondatrice de Toyota) à l’usine Ford de River Rouge en 1950 a inspiré la création du système de production Toyota.
En rompant avec les méthodes traditionnelles, Toyota a adopté une approche de production basée sur la demande réelle plutôt que sur la capacité, minimisant les stocks et développant une flexibilité et une réactivité devenues des normes industrielles.
Via plusieurs mécanisme ingénieux, l’objectif d’Eiji Toyoda était d’identifier et de réduire 3 principaux obstacles ou écarts par rapport à l’allocation optimale des ressources au sein du système : muri, mura et muda.
La surcharge (muri)
La surcharge (muri) fait référence à une contrainte excessive imposée au système, conduisant souvent à des efforts excessifs, à des erreurs et à des coûts inutiles.
L’incohérence (mura)
L’incohérence (mura) se réfère aux variations et aux irrégularités dans le processus de production, ce qui peut entraîner des inefficacités, des temps d’attente et des difficultés à maintenir une production stable.
Les gaspillages (muda)
Les gaspillages (muda) comprennent différentes formes de gaspillage, notamment :
- Gaspillages de surproduction (la plus grande part des gaspillages)
- Gaspillage du temps (attente)
- Gaspillage des transports
- Gaspillage de la fabrication elle-même
- Gaspillage des stocks disponibles
- Gaspillage de gestes
- Gaspillage dû à la fabrication de produits défectueux
- Gaspillage dû à une mauvaise utilisation des employés
Les principaux objectifs du TPS
Il s’agit d’éviter les surcharges (muri) et incohérences (mura), et d’éliminer les gaspillages (muda).
Les effets les plus significatifs sur le processus de création de valeur sont atteints par la conception de processus capables de fournir les résultats requis en douceur ; en évitant des incohérences (mura).
Il est également crucial de veiller à ce que le processus soit aussi flexible que nécessaire, sans tension ni surcharge (muri) puisque cela génère des gaspillages (muda).
Enfin, les réductions des gaspillages (l’élimination de la muda) sont très précieuses.
Le système de production Toyota a été souvent comparé à essorer une serviette sèche. C’est un système d’élimination des gaspillage en profondeur…
Beaucoup de gens se contentent d’éliminer les gaspillages que tout le monde identifie comme des gaspillages. Mais il en reste encore beaucoup qui n’ont tout simplement pas encore été reconnus comme des gaspillage ou que les gens sont prêts à tolérer !
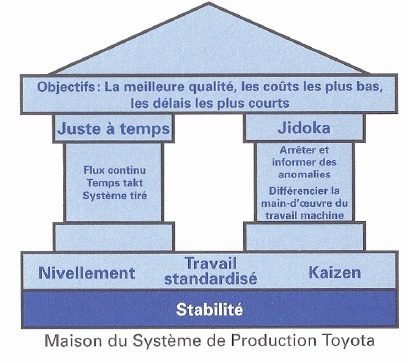
Le TPS repose sur 2 piliers conceptuels
- Le juste-à-temps : « Ne fabriquer que ce qui est nécessaire, seulement quand c’est nécessaire, et seulement dans la quantité nécessaire ».
- Le jidoka (Autonomie) : signifiant « Automatisation avec une touche humaine ».
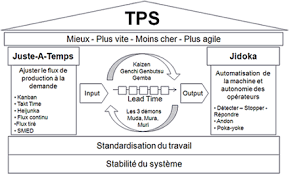
D’autres principes sous-jacents important du TPS
- L’amélioration continue via le Défi (vision à long terme, en relevant les défis avec courage et créativité pour réaliser ses rêves), le Kaizen (améliorer continuellement les opérations, en cherchant toujours à innover et à évoluer) et le Genchi Genbutsu (Aller à la source pour trouver les faits afin de prendre les bonnes décisions).
- Respect des personnes et Travail d’équipe (respect des autres, comprendre, assumer ses responsabilités et faire de notre mieux pour établir une confiance mutuelle tout en stimulant la croissance personnelle et professionnelle.
Principaux outils et concepts clés utilisés au sein du TPS
- Andon (行灯) (un grand tableau lumineux utilisé pour alerter les surveillants d’un problème à une station spécifique. Littéralement : enseigne)
- Gemba (現場) (l’endroit, le lieu où le vrai travail est fait ; sur le site)
- Genchi Genbutsu (現地現物) (allez voir par vous-même)
- Hansei (反省) (auto-réflexion)
- Heijunka (平 准 化) (le Lissage de la production)
- Jidoka (自 働 化) (autonomation – automatisation avec l’intelligence humaine)
- Juste-à-temps (ジャストインタイム)
- Kaizen (改善) (amélioration continue)
- Supermarché de fabrication où tous les composants sont disponibles pour être retiré par un processus
- Muda (無駄, aussi ムダ) (en français : gaspillages)
- Mura (斑 ou ムラ) (les aspérités)
- Muri (無理) (surcharge)
- Nemawashi (根回し) (construire les fondements, le consensus, littéralement : aller autour des racines)
- Obeya (大部屋) (réunion de managers, littéralement : grande chambre, salle de guerre, salle du conseil)
- Poka-yoke (ポカヨケ) (prévenir, pour éviter (yokeru) des erreurs involontaires (poka)
- Seibi (préparer)
- Seiri (整理) (trier, enlever ce qui n’est pas nécessaire)
- Seiton (整頓) (organiser)
- Seiso (清掃) (nettoyer et inspecter)
- Seiketsu (清潔) (standardiser)
🚨 Ne manquez pas les derniers articles dondon.media sur le Japon : sur Google Actualités, X, E-mail ou via notre flux RSS.